Nahaufnahme einer Hohlprägewalze. Quelle: Fraunhofer IWU
Wasserstoffsysteme, wie Brennstoffzellen und Elektrolyseure, arbeiten mit Bipolarplatten, die sich bislang nur aufwändig herstellen lassen. Fraunhofer Forscher wollen dies ändern.
Wasserstoff-Brennstoffzellen nutzen Wasserstoff und Sauerstoff, um Strom zu produzieren und damit etwa den Elektromotor von Brennstoffzellen-Fahrzeuge anzutreiben. In einem Brennstoffzellenstack ermöglicht der doppelwandige Aufbau der Bipolarplatten − kurz BPP
− das Strömen von Sauerstoff und Wasserstoff zu beiden Seiten der Membran und eine Wasserkühlung des Stacks. Das Problem: Die teure Herstellung der BPP bremsen derzeit die Anwendung der Wasserstofftechnologie und somit den breiten und kostengünstigen Einsatz von Brennstoffzellen-Fahrzeugen aus.
Einen Schritt in Richtung BPP-Massenproduktion gehen Forscher des Fraunhofer-Instituts für Werkzeugmaschinen und Umformtechnik (IWU) mit ihrer Entwicklung − der sogenannten „BPPflexRoll“. Bislang werden BPP in einer sogenannten Batch-Fertigung hergestellt. Das heißt, in Prozessen, die streng nacheinander abgearbeitet werde, man spricht auch von einem „Chargenprozess“. Mit ihrer Prototypen-Anlage, die die Chemnitzer Forscher zusammen mit der Profiroll Technologies GmbH aus Bad Düben, nördlich von Leipzig, entwickelt haben, wird diese Art der Fertigung abgelöst von einem kontinuierlich verlaufendem Hohlprägewalzverfahren.
Stefan Polster, Leiter der Gruppe „Blechbearbeitung und Werkzeugauslegung“ am Fraunhofer IWU erläutert: „Bipolarplatten bestehen aus jeweils zwei Edelstahl-Halbplatten, auf die in einem diskontinuierlichen Umformungsprozess Strukturen für den Gasfluss und die Wärmeabfuhr geprägt und die dann gefügt werden. Unser Hohlprägewalzverfahren hat das Potenzial, diese diskontinuierlichen Prozessketten beziehungsweise Fertigungsschritte durch ein kontinuierliches Verfahren abzulösen, das ohne Verfahrenspausen auskommt und damit eine hohe Stückzahlausbringung erlaubt.“
Ein Vorteil des Hohlprägewalzens sei insbesondere die höheren Prozessgeschwindigkeiten, wie Robin Kurth ergänzt. „Pro Minute lassen sich bis zu 120 BPP-Halbplatten fertigen“, so der Gruppenleiter für Umformmaschinen am Fraunhofer IWU. Durch die Umstellung des Herstellungsverfahrens wollen die Forschenden die Herstellungskosten für die BPP eigenen Angaben nach halbieren.
Kleinere Anlagentechnik notwendigDie Struktur der BPP wird, wie die Forscher erklären, mithilfe eines Walzenpaars geprägt. In diesem ist ein hauchdünnes Metallband eingespannt, das kontinuierlich durch die Anlage läuft. Die eine der beiden Umformwalzen ist als Stempel, die andere als Matrize definiert. Da die Walzen zum Ausformen der Strömungskanäle mit dem Werkstück annähernd nur einen Linienkontakt haben, lassen sich die Prozesskräfte im Vergleich zum konventionellen Hohlprägen durchschnittlich um den Faktor 10 reduzieren. Dies führt zu einer kleineren, kostengünstigeren Anlagentechnik.
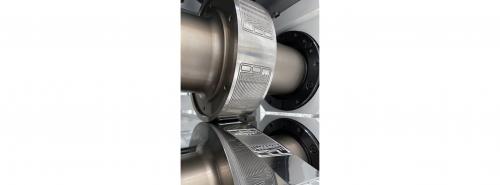 |
Mithilfe des von Fraunhofer und Profiroll Technologies entwickelten Prototypen wird die Struktur der Bipolarplatte durch ein Walzenpaar geprägt Quelle: Fraunhofer IWU |
Als weiteren Vorteil der Anlage, die am Fraunhofer IWU im Einsatz ist, nennen die Forscher deren Flexibilität: Die Anzahl der erforderlichen Walzensätze lässt sich in Abhängigkeit der BPP-Geometrie individuell anpassen.
Das Forscherteam arbeitet auch daran, ihre Anlage mittels Sensorik und Algorithmen intelligent zu machen. Sie soll in der Lage sein, sich selbst überwachen und steuern zu können, wie Kurth erklärt. „Anders als bei bisherigen Anlagen überprüfen wir künftig die Qualität der BPP im laufenden Prozess, indem wir die Prozessparameter mit Sensoren erfassen, zusammenführen und korreliert analysieren können“. Über Cloudlösungen sollen die gewonnenen Daten verarbeitet und nutzbar gemacht werden. Erste mit der Anlage produzierte BPP werden bereits am Fraunhofer-Institut für Solare Energiesysteme ISE in Freiburg in Brennstoffzellen getestet.
Ihren Prototypen „BPPflexRoll“ stellen die Forscher auf der Hannover Messe (22. bis 26. April) auf dem Fraunhofer-Gemeinschaftsstand in Halle 2, Stand B24 vor.
Mittwoch, 3.04.2024, 09:16 Uhr
© 2024 Energie & Management GmbH